Investors
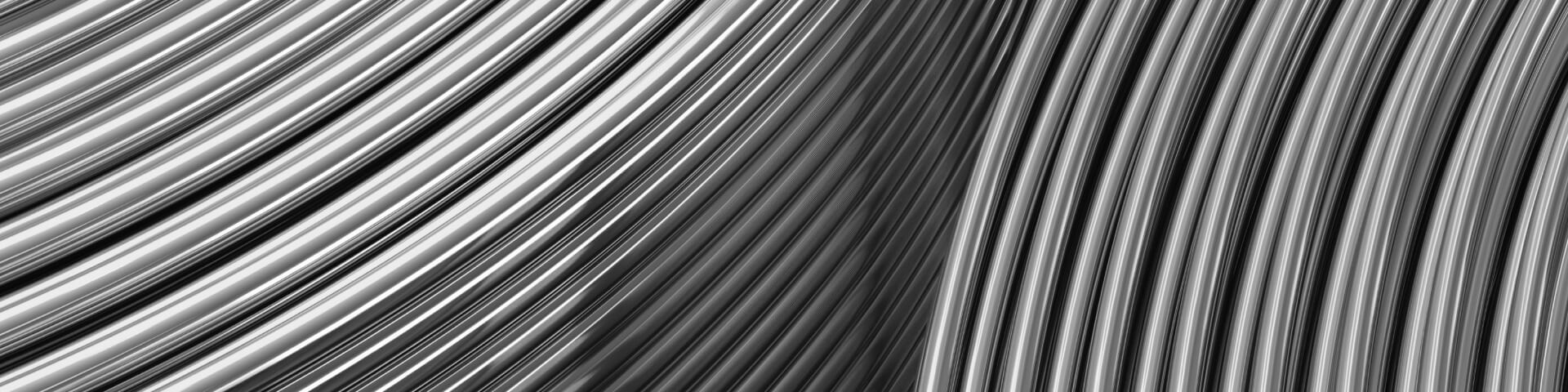
In the field of research and development, En+ Group combines its own competences and external expertise to achieve the best results and ensure a leading position in the industry.
The research and development competencies of our Metals segment are concentrated in research centers and institutes: Institute of Light Materials and Technologies (ILM&T); Russian Aluminum and Magnesium Institute; Siberian Scientific Research and Design and Design Institute of the Aluminum and Electrode Industry; Engineering and Technology Centre (RUSAL ETC).
Power segment is actively developing relationships with research institutes, universities, research centers, as well as companies that help bring new products and services to the market. The Group continues to cooperate with Moscow State University and Irkutsk National Research Technical University. Recently, Power segment joined the consortium of the Competence Center in the field of technologies for new and portable energy sources as part of the Institute of Problems of Chemical Physics of RAS to develop cooperation in the field of hydrogen energy and energy storage.
Perovskite solar tech
En+ Group is involved in the development of an exciting new generation of solar panels, in collaboration with Moscow State University. The project uses Perovskite solar cell technology, a new form of synthetic analogue which has proven highly efficient in converting solar energy into electricity, which could prove essential in meeting increased global energy demand.
The Group is carrying out a range of research which we hope will lead to the creation of a prototype — the first production sample of a perovskite solar cell with the necessary characteristics for wider industrial production.
Inert anode
Oxygen instead of carbon dioxide: this is the essence of the revolutionary inert anode technology.
In the production of aluminum, carbon anodes are used today, which during the electrolysis emit greenhouse gases (CO and CO2), polyaromatic hydrocarbons, benzopyrene and sulfur. Moreover, such anodes melt during aluminum production and require regular replacement.
The metallurgical segment En + Group is developing new material to create an inert anode. Not only the new technology prevents oxidizing (which will reduce costs), it will completely eliminate harmful emissions. Moreover, oxygen will be emitted instead of greenhouse gases: one electrolyzer using inert anode technology can produce as much oxygen as 70 hectares of forest.
Test production launched at the Krasnoyarsk aluminum smelter En+ Group. The experimental production of inert anodes is carried out at the Company's facility in Achinsk.
RA-550 technology
A benchmark among reduction cells: proprietary technology of En + Group's Metals segment reduces energy consumption and emissions.
Reduction cells based on RA-550 technology are capable of operating with a current strength of more than 500 kA (for comparison, the maximum current in a home outlet is 16 A). At the same time, energy consumption is 10-15% less than electricity compared to the previous generation ones — less than 13 kW / h per kilogram of aluminum. Another advantage of the new technology is the degree of purification of exhaust gases — up to 99%. Finally, the RA-550 has outstanding metal production: about 4 tons per day, which is 2 times more than RA-300.
RA-550 electrolyzers are used at the Sayanogorsk aluminum smelter of the Group. The company plans to expand the application of technology to other enterprises.
Leading specialists in the global aluminum industry, the RA-550 technology is today recognized as a reference solution in the field of aluminum electrolysis. Several companies from different regions of the world conduct with negotiations on its acquisition RUSAL.
Scandium oxide
Creation of unique alloys from production waste. En+ Group’s Metals Segment has developed a technology for the extraction of scandium from red mud (a by-product of alumina production).
Scandium is an element that literally enhances everything it touches. For example, in metallurgy, the addition of a small amount of scandium increases the strength of aluminum by 35%, and to chromium, it increases oxidation resistance up to a temperature of 1290 ° C. Yttrium scandate is one of the best materials for structures operating at high temperatures: withstands temperatures above 1000 ° C. These properties have made scandium a sought-after element in all industries where the strength of metal is needed — from motorcycle helmets to shipbuilding.
En + Group engineers have developed a unique technology for the extraction of scandium oxide from red mud, adapted to the alumina production process.
An industrial site for the production of scandium oxide was launched at the Urals aluminium smelter, where a product with a purity of 99.4% is produced.
Contacts
For investors
IR Department
For media
PR Department